- Dowel Insertion Machine Eliminates Human Error
- Design Casing Tool for Ergonomics & Sanitation
- Fully Automated Inspection Ensures Quality
- Quality Inspection, Service Delivers Results
- Rebuild Capabilities Save Flawed Machines, Money
- A Flexible Manufacturing Solution
- Reduction of Lead Time for Manufacturer of Bend Dies
- Automated Strip Part Chopper
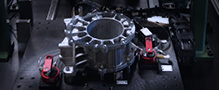
Alaark Tooling and Automation rose to the challenge and developed a high quality piece of equipment while conforming to an extremely tight deadline and ultimately exceeded original expectations.
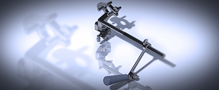
Working together with safety, sanitation and end users, we designed a tool with two objectives: meet higher sanitation standards in addition to eliminating negative ergonomic effects on the machine operator.
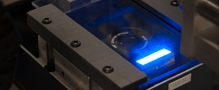
A manufacturer of machined aluminum die cast auto engine parts needed an inspection system built to inspect and verify 128 separate features on multiple sides of an engine part. Challenge accepted.
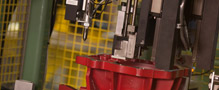
The key to building a machine to meet the client’s demands depended on engineering expertise, extreme attention to detail and constant communication between Alaark and the client.
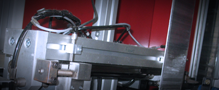
Flawed machines began to cost a client more than their overall worth. Alaark studied the machines and devised one temporary and one long-term solution that allowed to client to recover cost.
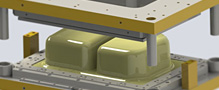
The simple, yet more costly solution would have been to build two separate dies to manufacture the stainless steel sinks. Alaark's engineers got the job done with only one.